We provide an overview of a NASA University Leadership Initiative project entitled “Development of an Ecosystem for Qualification of Additive Manufacturing Processes and Materials in Aviation”. This involved multiple universities and other collaborators working together to build a quantitative connection between AM processing, microstructure and properties in laser powder bed fusion of Ti-6Al-4V. Microstructure focused on defect structure and the key property was fatigue. The key result was that a) the defect content varied systematically across power-velocity space and was anti-correlated with fatigue life. The resulting process window was narrow compared to typical presentations. Printing the same set of 4-point bend fatigue bars in different machines at different sites produced similar results. Hypotheses are offered for the observed variations based on spatter rates and melt pool variability. We conclude that establishing a qualified materials process is feasible via an efficient survey of a limited domain of process space. This work provides the base for a newly started NASA Science & Technology Research Institute “Institute for Model-Based Qualification & Certification of Additive Manufacturing (IMQCAM)” that will create a numerical digital twin (DT) for fatigue. Uncertainty Quantification is a major focus for the team which has already revealed a significant sensitivity to feedstock variations, for example. Several component models exist such as microstructure prediction in Ti64 and 718 as well as microstructure-sensitive fatigue but linking models together in the DT requires substantial effort in terms of data exchange.
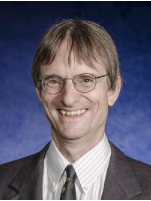
Rollett's research focuses on the science of additive manufacturing, 3D printed heat exchangers, microstructural evolution and microstructure- property relationships in 3D. Interests include microstructure control in 3D printing of metals, materials for energy conversion systems, strength of materials, constitutive relations, microstructure, texture, anisotropy, grain growth, recrystallization, formability, extreme value statistics and stereology. Important recent results include relating fatigue performance in printed Ti-6Al- 4V to LPBF parameters, machine learning to predict porosity development with synchrotron visualization as ground truth, development of a spectral approach to eigenstrain problems, validation of the 3D elasto-viscoplastic FFT code against synchrotron x-ray diffraction data, prediction of solidification microstructure, the appearance of new grains during grain growth, and grain size stabilization. He is a University Professor and the U.S. Steel Professor of Metallurgical Engineering and Materials Science at Carnegie Mellon University and a University Professor. He is a Fellow of several professional societies. He is the PI and co-Director of a NASA STRI on Institute for Model-Based Qualification & Certification of Additive Manufacturing (IMQCAM). He is also a co-Director of CMU’s NextManufacturing Center that is dedicated to advancing manufacturing especially through 3D printing of metals. He was awarded the ASM Gold Medal in 2024 and has over 330 peer-reviewed publications.